Поручни, EHS и непрерывные улучшения - как устроена система безопасности труда у ведущих мировых компаний
Поручни, EHS и непрерывные улучшения - как устроена система безопасности труда у ведущих мировых компаний

Мне доводилось бывать на многих предприятиях в разные годы. Могу отметить, что ситуация постепенно улучшается. Но яркие примеры достойной системы промышленной безопасности и охраны труда – редкость даже сегодня.
ЗАО «Завод Минплита» группы «Сен-Гобен» в Челябинске – очень впечатляющий пример. По крайней мере, такого количества плакатов и наклеек с призывом держаться за поручни (базовая норма безопасности в группе «Сен-Гобен») на каждом лестничном пролёте я точно не видел нигде. И даже гости здесь попадают в действующий цех только после видеоинструктажа по технике безопасности, переодевшись в спецодежду и обувь.
Чтобы узнать подробнее об опыте внедрения системы безопасности на производстве в группе «Сен-Гобен», входящей в Forbes TOP-100 крупнейших индустриальных компаний мира, я встретился с Евгением Прокопьевым, руководителем направления EHS (environment, health & safety – окружающая среда, здоровье и безопасность) на челябинском заводе минплиты.
Принцип «safety first» в «Сен-Гобен» реализован не на словах, а на деле – с него начинается каждое предприятие группы. Так и при покупке завода в Челябинске (2011г.), одними из первых инвестиций стали порядка 100 млн.руб. в улучшение условий и охраны труда: быт, спецодежда, безопасная организация производственных пространств и оборудования.
Материальная база – исходное условие. А самое главное и самое трудное – это поменять поведение работников, сломать опасные привычки и стереотипы, измененить сам образ мыслей. От принудительного исполнения стандартов под жестким контролем перейти к искреннему принятию людьми новых ценностей в сфере их же собственной безопасности. Фантастика? Лишь отчасти.
Евгений Прокопьев сам работал прежде на другом предприятии данной отрасли, типичном для нашей производственной практики – со сдельной оплатой труда, с минимальными условиями быта и с «авось» вместо безопасности. Раньше это казалось удобным, привыкать к новым строгим нормам было трудно. Но со временем огромная польза такой жёсткой системы стала очевидной, появилось искреннее желание передавать такой подход новым работникам. Позднее, благодаря такому стремлению, накопленным компетенциям и успехам, Евгений был назначен на должность менеджера EHS.
Алгоритм формирования культуры максимальной безопасности на производстве приблизительно следующий:
1) Формирование ведущей лидерской позиции руководителей.
Каждый должен являть собой безупречный пример соблюдения стандартов безопасности и быть внимательным наставником для остальных.
Все начинается с подбора и перевоспитания команды топ-менеджмента, затем управленцы среднего звена и так далее.
2) Устранение мотивации к нарушениям норм безопасности.
По мнению «Сен-Гобен», такой мотивацией является сдельная оплата труда – ради наращивания объемов работники пренебрегают соблюдением стандартов и технологий. Поэтому на предприятиях группы применяется только окладная система.
3) Воспитание вместо наказания – компания не приемлет штрафы, как демотивирующий и разрушающий лояльность фактор.
Работников поддерживают, поощряют, регулярно учат, им помогают и разъясняют. Для значительной части российского менеджмента такой подход пока непонятен, но это опыт мировых лидеров.
Собственно и те замечания, которые я неоднократно получал от сопровождающих меня сотрудников завода за то, что по привычке не держался за перила лестницы, – это прежде всего элемент воспитания, усиление внимания к безупречному соблюдению стандартов безопасности, даже в части самых элементарных и, казалось бы, пустяковых норм.
Такие же строгие требования предъявляются ко всем подрядчикам – не должно быть такого, что одни работники в цехе соблюдают стандарты, а другие нет. Неважно кто из какой организации, это вопрос укрепления общей дисциплины.
На заводе внедрена система организации рабочих мест 5S – каждый инструмент хранится на своем размеченном месте на специальном стенде, нигде ничего лишнего. Помимо экономии и организации труда, это тоже часть общей дисциплинирующей системы, нацеленной на соблюдение стандартов качества и безопасности.
4) Вовлечение работников в процесс непрерывных улучшений безопасности – вся система постоянно совершенствуется при активном участии каждого сотрудника компании.
Это часть внедренных на предприятии принципов WCM (World Class Manufacturing), целью которых является достижение так называемых «трех нулей»: ноль несчастных случаев, ноль задержек (в т.ч. поломок, внеплановых простоев, задержки поставок товара потребителям) и ноль брака.
В основе WCM лежат 2 основных принципа: постоянное совершенствование и устранение потерь.
Цикл «планируй-делай-проверяй-улучшай» выполняет каждый работник в рамках своих обязанностей.
В части безопасности этот цикл представляет собой поиск каждым работником ситуаций риска (инцидентов) и последующее их устранение (самостоятельное ограждение опасной зоны и доклад руководству). Ситуации риска разделены на пять групп:
TF1, TF2 и TF3 – касаются инцидентов, фактически повлекших производственные травмы;
TF4 – случившийся инцидент (авария), создавший угрозу безопасности, но не повлекший травм;
TF5 – назревающая опасная ситуация, которая впоследствии может привести к инциденту.
Все случаи выявления ситуаций риска отражаются на специальных информационных стендах, размещенных в каждом цехе (см. фото).
Основной драйвер, поддерживающий данную систему в активном состоянии – еженедельные совещания по теме безопасности с обсуждением всех предложений работников. Ключевой акцент – это выявление TF5.
5) Проведение специальных акций по укреплению корпоративной культуры в части охраны труда и промышленной безопасности.
Яркий пример – это День EHS «Сен-Гобен», о котором я уже рассказывал (ссылка).
Самый главный фактор для успешного внедрения всех упомянутых практик – это постоянное внимание и настойчивость, исходящие от директора и ТОП-менеждмента предприятия, и далее транслируемые через всю иерархию до каждого работника.
Успешным внедрением можно считать момент достижения некоей критической массы в коллективе, когда преобладающая часть работников начинает разделять ценности и принципы этой системы, и уже самостоятельно передает их остальным.
Собственно и у нас в регионе тоже хорошо бы достичь некоей критической массы – когда большинство предприятий внедрит у себя лучшие практики высокой культуры производства, а остальные за ними подтянутся, чтобы сохранить конкурентоспособные позиции. Будем надеяться, в ближайшем будущем это произойдет.
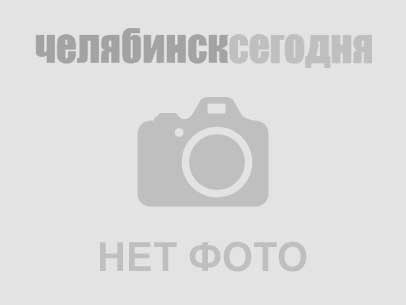
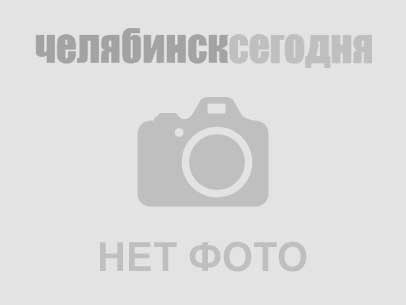
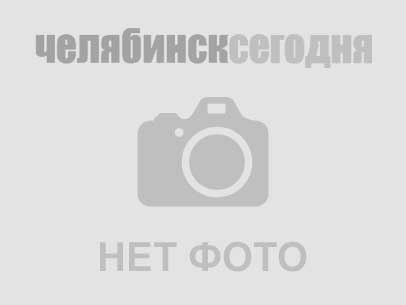
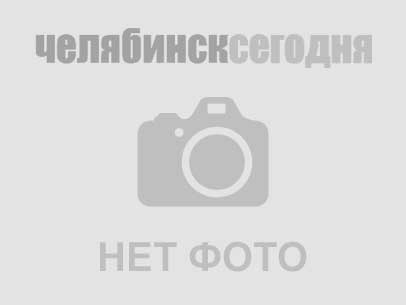
ЗАО «Завод Минплита» группы «Сен-Гобен» в Челябинске – очень впечатляющий пример. По крайней мере, такого количества плакатов и наклеек с призывом держаться за поручни (базовая норма безопасности в группе «Сен-Гобен») на каждом лестничном пролёте я точно не видел нигде. И даже гости здесь попадают в действующий цех только после видеоинструктажа по технике безопасности, переодевшись в спецодежду и обувь.
Чтобы узнать подробнее об опыте внедрения системы безопасности на производстве в группе «Сен-Гобен», входящей в Forbes TOP-100 крупнейших индустриальных компаний мира, я встретился с Евгением Прокопьевым, руководителем направления EHS (environment, health & safety – окружающая среда, здоровье и безопасность) на челябинском заводе минплиты.
Принцип «safety first» в «Сен-Гобен» реализован не на словах, а на деле – с него начинается каждое предприятие группы. Так и при покупке завода в Челябинске (2011г.), одними из первых инвестиций стали порядка 100 млн.руб. в улучшение условий и охраны труда: быт, спецодежда, безопасная организация производственных пространств и оборудования.
Материальная база – исходное условие. А самое главное и самое трудное – это поменять поведение работников, сломать опасные привычки и стереотипы, измененить сам образ мыслей. От принудительного исполнения стандартов под жестким контролем перейти к искреннему принятию людьми новых ценностей в сфере их же собственной безопасности. Фантастика? Лишь отчасти.
Евгений Прокопьев сам работал прежде на другом предприятии данной отрасли, типичном для нашей производственной практики – со сдельной оплатой труда, с минимальными условиями быта и с «авось» вместо безопасности. Раньше это казалось удобным, привыкать к новым строгим нормам было трудно. Но со временем огромная польза такой жёсткой системы стала очевидной, появилось искреннее желание передавать такой подход новым работникам. Позднее, благодаря такому стремлению, накопленным компетенциям и успехам, Евгений был назначен на должность менеджера EHS.
Алгоритм формирования культуры максимальной безопасности на производстве приблизительно следующий:
1) Формирование ведущей лидерской позиции руководителей.
Каждый должен являть собой безупречный пример соблюдения стандартов безопасности и быть внимательным наставником для остальных.
Все начинается с подбора и перевоспитания команды топ-менеджмента, затем управленцы среднего звена и так далее.
2) Устранение мотивации к нарушениям норм безопасности.
По мнению «Сен-Гобен», такой мотивацией является сдельная оплата труда – ради наращивания объемов работники пренебрегают соблюдением стандартов и технологий. Поэтому на предприятиях группы применяется только окладная система.
3) Воспитание вместо наказания – компания не приемлет штрафы, как демотивирующий и разрушающий лояльность фактор.
Работников поддерживают, поощряют, регулярно учат, им помогают и разъясняют. Для значительной части российского менеджмента такой подход пока непонятен, но это опыт мировых лидеров.
Собственно и те замечания, которые я неоднократно получал от сопровождающих меня сотрудников завода за то, что по привычке не держался за перила лестницы, – это прежде всего элемент воспитания, усиление внимания к безупречному соблюдению стандартов безопасности, даже в части самых элементарных и, казалось бы, пустяковых норм.
Такие же строгие требования предъявляются ко всем подрядчикам – не должно быть такого, что одни работники в цехе соблюдают стандарты, а другие нет. Неважно кто из какой организации, это вопрос укрепления общей дисциплины.
На заводе внедрена система организации рабочих мест 5S – каждый инструмент хранится на своем размеченном месте на специальном стенде, нигде ничего лишнего. Помимо экономии и организации труда, это тоже часть общей дисциплинирующей системы, нацеленной на соблюдение стандартов качества и безопасности.
4) Вовлечение работников в процесс непрерывных улучшений безопасности – вся система постоянно совершенствуется при активном участии каждого сотрудника компании.
Это часть внедренных на предприятии принципов WCM (World Class Manufacturing), целью которых является достижение так называемых «трех нулей»: ноль несчастных случаев, ноль задержек (в т.ч. поломок, внеплановых простоев, задержки поставок товара потребителям) и ноль брака.
В основе WCM лежат 2 основных принципа: постоянное совершенствование и устранение потерь.
Цикл «планируй-делай-проверяй-улучшай» выполняет каждый работник в рамках своих обязанностей.
В части безопасности этот цикл представляет собой поиск каждым работником ситуаций риска (инцидентов) и последующее их устранение (самостоятельное ограждение опасной зоны и доклад руководству). Ситуации риска разделены на пять групп:
TF1, TF2 и TF3 – касаются инцидентов, фактически повлекших производственные травмы;
TF4 – случившийся инцидент (авария), создавший угрозу безопасности, но не повлекший травм;
TF5 – назревающая опасная ситуация, которая впоследствии может привести к инциденту.
Все случаи выявления ситуаций риска отражаются на специальных информационных стендах, размещенных в каждом цехе (см. фото).
Основной драйвер, поддерживающий данную систему в активном состоянии – еженедельные совещания по теме безопасности с обсуждением всех предложений работников. Ключевой акцент – это выявление TF5.
5) Проведение специальных акций по укреплению корпоративной культуры в части охраны труда и промышленной безопасности.
Яркий пример – это День EHS «Сен-Гобен», о котором я уже рассказывал (ссылка).
Самый главный фактор для успешного внедрения всех упомянутых практик – это постоянное внимание и настойчивость, исходящие от директора и ТОП-менеждмента предприятия, и далее транслируемые через всю иерархию до каждого работника.
Успешным внедрением можно считать момент достижения некоей критической массы в коллективе, когда преобладающая часть работников начинает разделять ценности и принципы этой системы, и уже самостоятельно передает их остальным.
Собственно и у нас в регионе тоже хорошо бы достичь некоей критической массы – когда большинство предприятий внедрит у себя лучшие практики высокой культуры производства, а остальные за ними подтянутся, чтобы сохранить конкурентоспособные позиции. Будем надеяться, в ближайшем будущем это произойдет.
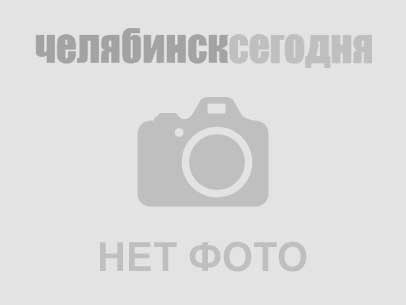
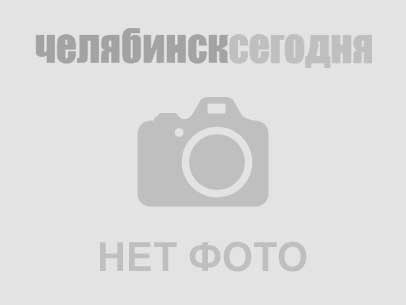
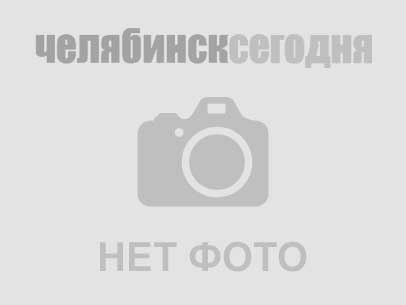
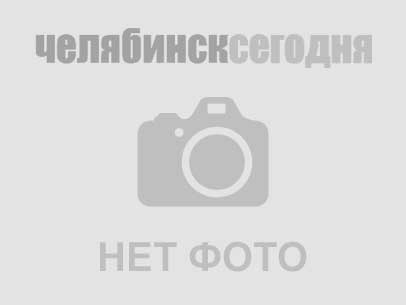